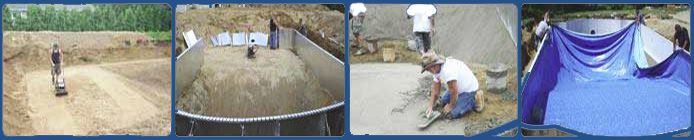
Installing an inground pool kit in your backyard is something that will bring a lot of personal pride, being able to tell your friends that you are building your own inground pool. An inground pool adds value to the home, and brings the family (and the neighborhood) together.
But – it’s not without complications. Building your own inground pool can be done in just 4-5 days, if you have all of your ‘ducks’ in a row. This blog, and your SPP Pool Experts, are an unlimited and free resource for our pool kit customers – most of whom avail themselves of the information and expertise.
For some DIY pool builders, those who throw away the instructions, and dive right in – there are some pitfalls waiting for you. Here’s 5 specific mistakes to avoid when building an inground pool yourself.
NOT LEVELING THE POOL WALLS
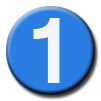
Getting your pool walls to be both level and plumb takes some time, but it’s well worth it. If the walls are not all exactly the same height, or if some wall sections are leaning slightly inward, or outward – this mistake can not only be visible, but it can put stress on the wall panels and the pool deck.
Larry wrote a great blog post on using a transit to level the pool walls, and describes in detail how to make sure that the wall panels are all vertical, or plumb. Using a transit or sight level will take a few minutes to master, but once you do – you can make quick work of checking each wall panel. You’ll do it more than once. When the panels are being rough installed, then after the panels are tightened up, and the braces installed. Immediately after pouring the concrete collar, you should check the walls again, to be sure that the process of pouring the concrete foundation around the base of the walls, has not shifted the panels, even slightly. Before concrete hardens, you have an hour or two to check again, and make adjustments if necessary.
NOT LEVELING THE FLOOR
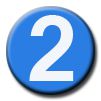
“Eyeballing” the pool floor, without using ‘Stakes and Strings‘ can result in a floor that is uneven – low in some spots, high in others. This may not be so readily visible underwater, until you turn the pool light on, at night. Then it really jumps out at you, casting shadows, and highlighting every imperfection.
Larry also wrote a blog post on Buying, Mixing and Applying Vermiculite to the pool floor, with some tips on using strings to help you keep the height of the floor consistent, and also to help define the transitions between the different floor areas. Some of it is actually ‘eyeballing’ it, especially across the middle of the pool floor, so make sure you get a second set of eyes looking at it. Before the floor hardens, you can shave high spots with the edge of your trowel, or move more floor material to fill in low spots. Vermiculite is very lightweight and easy to work with, just take your time, and look at it from all angles, as you proceed, starting in the deep end, eventually working your way out of a shallow end corner.
CUTTING IN THE LINER TOO EARLY
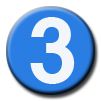
Cutting in the liner refers to installing the skimmer, return and pool light faceplates, and then cutting out the vinyl inside of the faceplate. If done too early, before the liner has had a chance to fully stretch, the screw holes can open up and cause a leak, or worse, it can rip the liner in that area.
To avoid such a problem, wait until the water level is just below ( or just above ) the pool light, skimmer or returns. The exception to this is of course the main drain. Once the liner has been set with a vacuum, and is positioned properly, you will install the main drain rings, cut out the vinyl and install the main drain covers. The step or swim out sections should not be cut-out until the water is over the shallow end floor. Placing sand bags under the step, on top of the liner, can help hold the liner in place, while the screws are installed on 3 sides of the step. For the underwater light, skimmer and returns, wait until the water is at or above, before you install the faceplates, or trim ring. It’s a simple thing, but some DIY pool builders, get a bit excited and ahead of themselves.
BACKFILLING BEFORE PLUMBING IS TESTED
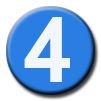
The usual process is to fill the pool with water, before you backfill up against the pool walls, and fill in the trench that runs from the pool to the pool equipment pad. If you want to backfill before starting the pool pump, you could pressure test the pipes, with water pressure.
Pressure testing involves some specialized plugs, nothing fancy. Call your SPP Pool Experts if you want to do this, or if you have a plumber doing the job, it’s a normal part of their work, to prove that there are no leaks in the job. Otherwise, if you can wait to backfill, start up the pool equipment after the pool is filled, and check it carefully before burying the pipes in several feet of earth, and then covering in concrete. Also pay attention to any leaks at the pool wall, drips running down the wall from the skimmer, returns, lights or steps. If any leakage is noticed in these areas, usually tightening up the screws, with a suitably large Phillips head screwdriver will solve the problem – assuming that the gaskets were not forgotten!
INSTALLING THE POOL DECK TOO SOON
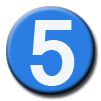
After backfilling, the soils around the pool need to settle into place. Generally, about 30 days, and a few rains or watering, will be sufficient time for the backfill to settle, before adding slabs of concrete on top. Pouring the deck too soon can result in an uneven or tilted pool deck.
Larry (once again!) wrote a recent blog post on Contracting a Concrete Pool Deck, and in it, he mentions a way to speed up the deck installation timeline. During backfill, his technique was to tamp the backfill material, every foot. That is, backfill a foot of dirt, and then tamp it with a mechanical tamper before adding the next foot. After this is done, he would use a sprinkler and soak the entire area for a day or two, tamp it again when it’s dry, and then add 4-6″ of gravel for the concrete pool deck to be placed.
Using this method, you can usually pour your pool deck within a week of backfilling. It’s funny, because when Larry built his own pool, he went months before pouring the deck! Not to allow full settling, but because he was still making a careful decision on the type and size of pool deck he (and his wife) wanted to install.
There you have it – 5 Mistakes to Avoid when building your own inground pool kit. There are more, and you can read about some other possible DIY pool construction blunders here, and if you have yet to buy your inground pool kit, read up on 5 mistakes to avoid when purchasing an inground pool kit.
Hi. My son’s new pool has sidestepped these 5 mistakes. Hoping to sidestep another. Pool company is done now. My son has 1-4′ concrete ‘collar’ and decking installed. He wants to put new sod around to meet the decking edge. What’s the best material to put down there? I guess the thing to avoid is having water get under the 3″ of decking concrete. He plans to angle the slope slightly so water drains away from the pool. Help on this would be appreciated as he’s ready to order the material for it. Small gravel? Soil? Peat? Thanks…
Hi Jana, just use top soil up against the pool deck, firmly tamped, and gently slope to a low spot, where you can create a gulley or swale along side the pool, that runs to one ends preferably, for continuous drainage. To help that end, dig down 12″ and place a 6″ perforated drain tile pipe, and bury that in small gravel all around the pipe, and top it with 3″ of soil, then sod.